Call us: +86-137-2353-4866
A force sensing resistor finds force by changing resistance when you press it. This sensor has two layers with a small space between them. When you push the layers together, resistance goes down. This lets electrical current move through. The link between force and resistance shows how fsr works. Force sensing resistors are used in many fields. They are thin, work well, and do not cost much.
Industry Use | Details |
---|---|
Automotive | Safety, touch controls |
Consumer Electronics | Smart devices, wearables |
Medical Devices | Monitoring, prosthetics |
Robotics | Automation, human interfaces |
Table of Contents
Key Takeaways
- Force sensing resistors (FSRs) find force by changing resistance when pressed. This helps us measure pressure or touch easily.
- FSRs have two main types: Shunt Mode and Thru Mode. Each type works best for different things, like airbags or robot fingers.
- The sensor is thin and flexible. It uses special materials that conduct electricity. This makes FSRs great for wearables, robots, and medical tools.
- FSRs use the piezoresistive effect. Pressing them lowers resistance and changes voltage. This lets us sense force quickly and easily.
- Important things for FSRs are sensitivity, range, response time, linearity, and durability. These affect how well the sensor measures force.
- FSRs are used in electronics, robots, medical devices, car safety, and sensor arrays. They help give better control and data.
- To connect an FSR, you use a voltage divider circuit with a fixed resistor. Microcontrollers like Arduino can read what the sensor says.
- To get good readings, install the sensor right, check it often, and take care of it. This helps the sensor last longer.
Force Sensing Resistor Basics
Definition
A force sensing resistor is a sensor that finds changes in force by changing its electrical resistance. This device is thin and can bend. It has a special ink or material between two layers. When you press the sensor, the resistance gets lower. More current can then move through it. Engineers use this technology to measure pressure or touch in many products. The force sensing resistor is special because it is thin, bends easily, and fits into many designs.
Note: Force sensing resistors have high resistance when no one presses them. When someone pushes on them, the resistance drops from very high to much lower. This makes them good for finding touch or pressure.
Principle
The main idea behind a force sensing resistor is called the piezoresistive effect. When you push on the sensor, the conductive layer touches the circuit. This makes the resistance go down. The link between resistance and force follows a power-law model. As you press harder, resistance keeps dropping in a way you can predict. You can see this in the chart below, which shows how different parts of the sensor react to force:
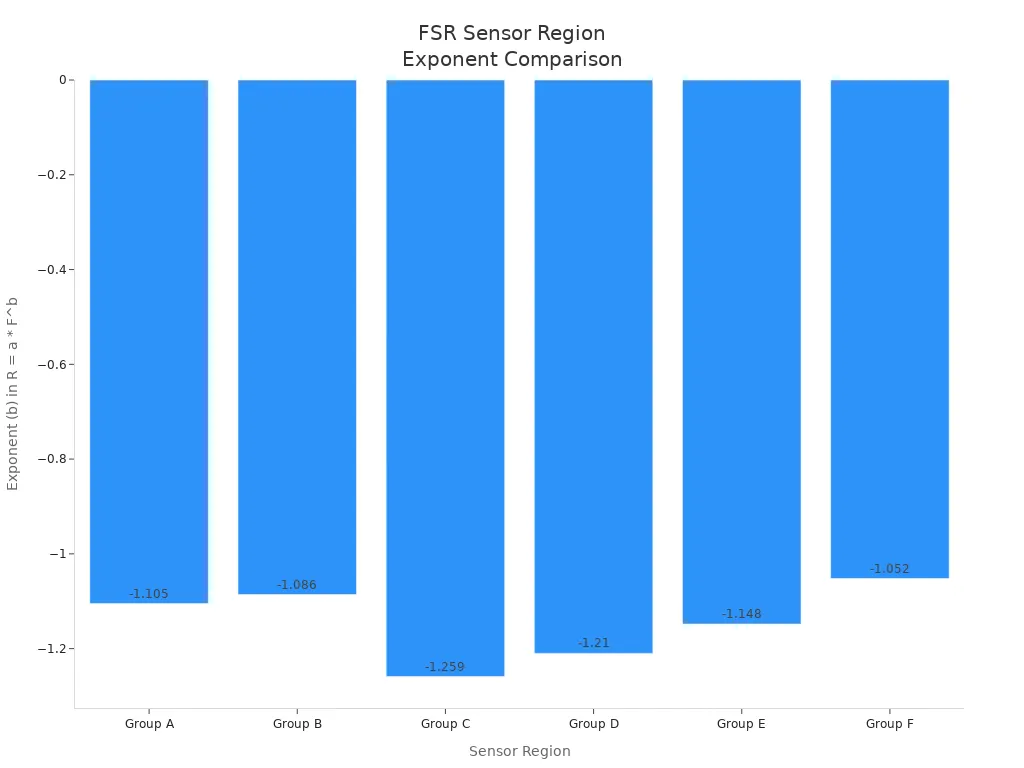
Researchers check this idea by using known forces and measuring what the sensor does. For example, they put the sensor on a curved pipe and use a voltage divider circuit to see changes. The sensor’s output matches the force they use, so the idea works. In robotics, the sensor can move a robot finger. It works well with small forces and does not use much power.
Types
There are different types of fsr. Each type has its own structure and use. The two most common types are Shunt Mode and Thru Mode. The table below shows how they are built and what makes them different:
Type of FSR | Structure Description | Key Structural Difference |
---|---|---|
Shunt Mode | Made with polymer thick-film. It has two parts with a spacer between them. When you press, the ink touches the electrodes and changes resistance. | Two parts with a spacer; resistance changes when ink touches under pressure. |
Thru Mode | Made from polyester film printed circuits on the outside. Conductive parts hold pressure-sensitive layers together, stuck with glue. | Polyester film layers glued together; conductive parts hold pressure-sensitive layers. |
Each type is good for different jobs. Shunt Mode types work well in car airbags, shoe insoles, and hospital beds. Thru Mode types are used in robot fingers, music controllers, and infusion pumps.
- The main types of fsr give you:
- Thin and bendy shapes
- Low power use
- Easy to add to circuits
- Custom shapes and sizes for special needs
Tip:
Pick the right type for your job. For example, Shunt Mode is good for pressure maps in shoes. Thru Mode works best for robot touch sensors.
Construction
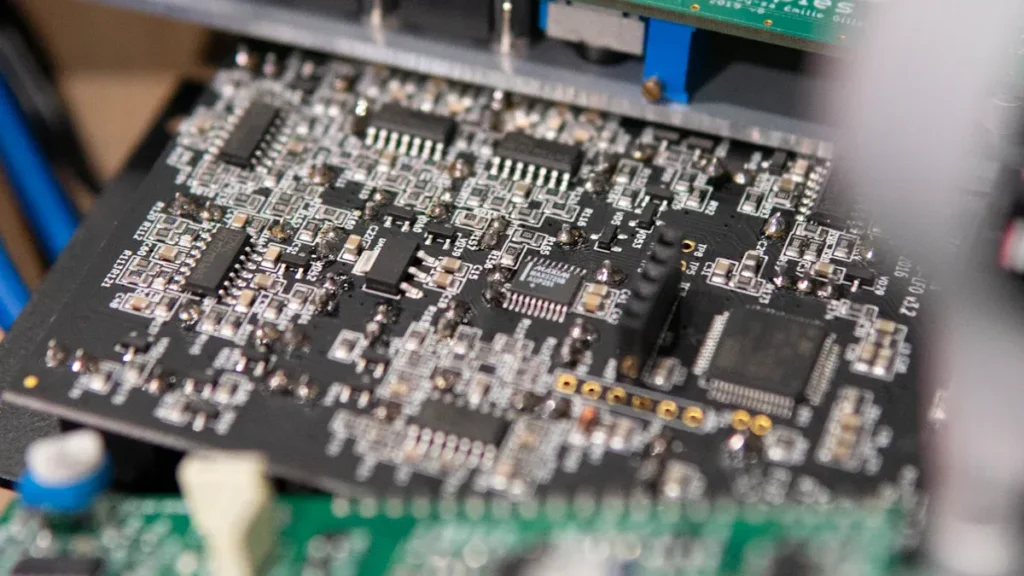
Structure
A force sensing resistor has layers that help it sense force. The SOUSHINE sensor uses a bendy base called a membrane substrate. This base holds two parts of a circuit that do not touch. Special ink covers the part that senses force. When you press down, the top layer touches the circuit. This closes the gap and lets electricity move. The sensor has:
- Electrodes that pick up electric signals.
- A sensing part made from a sheet that conducts electricity.
- A spacer that keeps layers apart until you press.
- An output circuit that turns resistance changes into signals you can read.
All these parts work together to turn pressure into an electric signal. This sensor is part of the resistive based sensor group. These sensors measure force by how much resistance changes.
Materials
Conductive Layers
The sensing layer uses special plastics that conduct electricity. These plastics have tiny bits that can and cannot carry electricity. When you press, the bits touch the electrodes and resistance drops. The SOUSHINE sensor uses special ink to make sure it works the same way every time. This material keeps the sensor thin and bendy. That makes it good for many uses.
Substrate
The substrate is the bottom part of the sensor. It is a flexible base, often made from polyester film. This makes the sensor strong and able to handle bumps. The base holds the ink and the electrodes in place. This design keeps the sensor light and easy to use in many products. Because the base is flexible, the sensor can fit in curved or small spaces.
Design Variations
Different designs change how force sensing resistors work in different places. The table below shows how shape, size, and materials change what the sensor can do:
Design Aspect | Impact on Performance and Application Suitability |
---|---|
Shape | Changes where you can put force and how you attach it. Round ones are good for buttons. Square ones are good for touchpads. |
Size | Changes how much area the sensor can sense. Small sensors are more exact. Big sensors cover more space. |
Material Composition | Changes how sensitive and tough the sensor is. Different materials make the sensor work better or last longer. |
Sensitivity | More sensitivity helps find smaller forces. |
Resistance Range | Changes how well the sensor measures force. |
Form Factor | Thin, bendy sensors fit in tight spots but can break easier. |
FSRs are a kind of resistive based sensor. They do not react in a straight line and need to be set up right for exact jobs. You can change their thickness, shape, and resistance range. This helps engineers pick the best sensor for each job.
Force sensing resistors are part of the piezoresistive sensor group. They are not like old strain gauges that use metal stretching to change resistance. FSRs use special materials that change how well they conduct electricity. This makes FSRs change resistance more and makes them great for bendy, wearable, and strong designs.
Working Principle
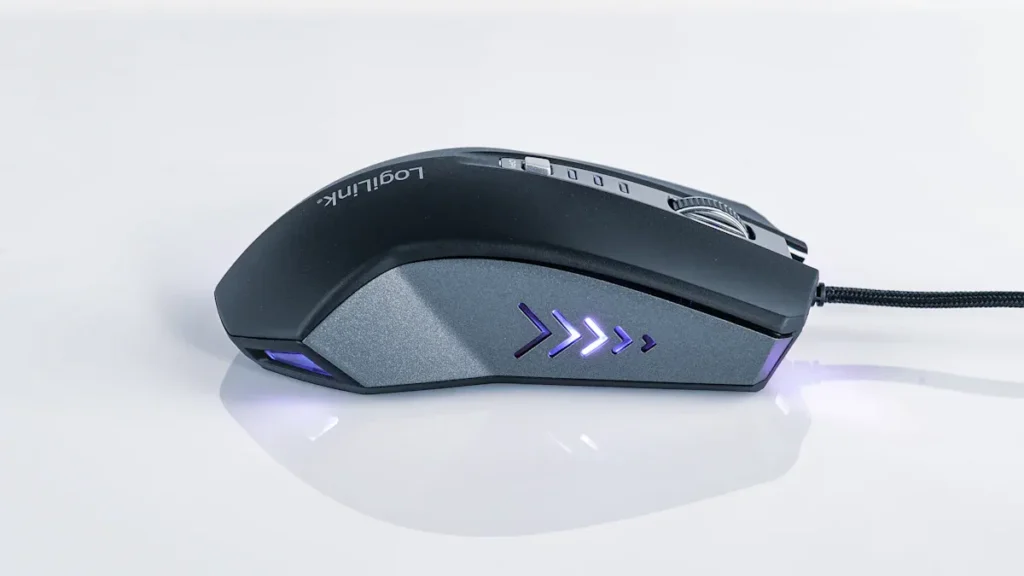
Piezoresistive Effect
A force sensing resistor works by using the piezoresistive effect. When you press on the sensor, the inside material changes how it lets electricity flow. This happens because the material acts differently when squeezed. Scientists use special numbers called piezoresistive coefficients to explain this. These numbers depend on what the sensor is made of and how it was built. When the resistance changes, the voltage across the sensor also changes. This lets the sensor tell how much force is being used by watching the resistance. The piezoresistive effect is the main reason fsr works in real life.
The piezoresistive effect helps the sensor turn a push into an electric signal. This makes it easy to measure touch, pressure, or weight with simple tools.
Resistance Change
The resistance in a force sensing resistor goes down when you press harder. When no one is pressing, the resistance is very high, over 1 megaohm. If you press a little, the resistance drops to about 100 kiloohms. If you press as hard as you can, it can go as low as 200 ohms. The resistance does not drop in a straight line. It falls fast at first, then slows down as it gets lower. The table below shows how resistance changes with different forces:
Applied Force | Resistance (Ω) |
---|---|
No applied pressure | > 1,000,000 (1 MΩ) |
20 grams weight | ~50,000 (50 kΩ) |
Maximum applied force | ~200 |
The sensor needs at least 20 grams of force to start working. As more of the sensor touches the conductive layer, the resistance keeps dropping. This makes the sensor good for knowing if there is force and how much, but not for measuring exact weights.
Electrical Output
A force sensing resistor gives an electrical signal that matches the force you use. The sensor connects to a circuit, often with a voltage divider. When resistance drops, the voltage across the sensor changes too. A microcontroller or other device can read this voltage. The sensor reacts in just a few milliseconds, so it is good for fast sensing. It works with voltages from 1V to 5V, which fits most electronics. The table below lists important electrical output features:
Characteristic | Description |
---|---|
Resistance Range | Several megaohms (no force) to a few hundred ohms (maximum force) |
Sensitivity | Change in resistance per unit force, measured in ohms/gram |
Minimum Actuation Force | About 20 grams needed to start sensing |
Output Measurement | Voltage divider circuit converts resistance to voltage |
Response Time | Milliseconds |
Repeatability | ±2% to ±5% |
Linearity | Non-linear; needs calibration for exact readings |
The sensor can sense forces from 20 grams up to 2 kilograms or more. It stays strong and works well even after millions of uses. The electrical output makes it simple to use the sensor in many projects, like touchpads or robot hands.
Key Parameters
Sensitivity
Sensitivity shows how well a force sensing resistor finds small force changes. Engineers use different ways to check this. These ways include drift, hysteresis, deadband, and linearity. Each one helps show how the sensor acts when pressed.
- Drift tells how much the sensor’s reading changes if you keep pressing with the same force. To test drift, engineers press as hard as the sensor allows and watch the voltage for about 45 seconds. They write down how much the voltage changes as a percent of the starting value.
- Hysteresis is the difference in what the sensor shows when you press and then let go. Engineers look at the voltage when pressing and when letting go. They find the biggest difference and write it as a percent of the whole voltage range.
- Deadband is the smallest force that makes the sensor react. Engineers slowly push harder until the sensor’s voltage changes. They show this as a percent of the total force the sensor can feel.
- Linearity shows if the sensor’s output goes up in a straight line as you press harder. Engineers press harder step by step and draw a straight line on a graph. They use a number called R² to see how close the data is to the line.
Engineers use rules like ANSI/ISA-51.1-1979 (R1993) for these tests. They use tools like force actuators, fake skin, and load cells to get good results. The type of circuit, like a voltage divider or amplifier, can change how sensitive the sensor seems.
Sensitivity checks help engineers pick the best sensor for each job. This makes sure the sensor works well in real life.
Range
The range tells the smallest and biggest forces a force sensing resistor can sense. Most sensors can measure from 0 Newtons up to 200 pounds, or about 0 to 890 Newtons. This big range lets the sensors work in many areas, like medical tools or factory machines. The low end means the sensor can feel soft touches. The high end means it can handle strong pushes or heavy things. Engineers pick the sensor based on how much force they expect to use.
Response Time
Response time is how fast a force sensing resistor reacts to new force. Most sensors react in just a few milliseconds. This quick action is good for things that need fast feedback, like touchpads or robot hands. A short response time means the system can notice and use force changes right away. Engineers test this by pressing and letting go quickly, then watching how fast the sensor’s output changes. Fast and steady response times are important for safety and for making products work well.
Linearity
Linearity means how well the output matches the force you use. If a sensor was perfect, the output would go up in a straight line as you press harder. But FSRs do not do this. Their output goes up in a curve, not a straight line. When engineers test FSRs, they see the output does not fit a straight line very well. The R² value is about 0.94, which is not perfect. If they use a third-order polynomial, the fit gets much better, with an R² of 0.997. This shows the link between force and output is not straight.
Many things change the linearity of FSRs:
- The part that carries electricity gets bigger as you press more. This makes the output less straight.
- The resistance inside the FSR depends on both force and voltage. This makes resistance change in a curvy way.
- The voltage output is tied to the opposite of the FSR resistance. Since resistance changes in a curve, so does the voltage.
- Hysteresis and repeatability problems can also make the output less straight.
Engineers can use special circuits and calibration to help linearity. These tricks help, but they cannot fix all the curvy effects. For most uses, FSRs still give a good signal when force changes, even if the output is not a perfect line. Designers should remember this when using FSRs in things that need exact force numbers.
Tip: Calibration and signal processing can help make FSR readings more accurate in jobs that need exact force measurement.
Durability
Durability tells how well a force sensing resistor works after many uses and in tough places. SOUSHINE FSRs do well in lots of tests. They keep steady resistance after over 1,000 presses at 0.5 Hz. This makes them good for switches and other jobs that need lots of pressing.
Aspect | Details |
---|---|
Loading/Unloading Cycles | Steady resistance after 1,000 cycles at 0.5 Hz |
Washability | Works well after 5 fast washes (like 25 normal washes) |
Extended Washability | Does not work as well after 10 fast washes because the membrane breaks |
Response Time | Fast, about 0.1 seconds when pressing and letting go |
Material Resilience | Textile and TPU parts keep working after many presses |
Pressure Range | Resistance stays steady under pressures over 100 kPa |
Comfort Properties | Air can still pass through after printing and lamination |
FSRs made with polymer can have problems in very hot, wet, or chemical places. High humidity, big temperature changes, or chemicals can make the sensor drift or stop working over time. In places like cars or outdoor robots, engineers add covers to help the sensor last longer. This helps, but can make the sensor less bendy and cost more.
Most SOUSHINE FSRs keep working well after lots of use. They react fast and bounce back quickly, so they are good for home and work products. The materials also keep the sensor comfy and let air through, which is good for things you wear. To get the best results, users should follow care tips and keep the sensor away from harsh chemicals or too much heat.
FSR Sensor Applications
Consumer Electronics
Consumer electronics use fsr sensor technology in many ways. These sensors help devices feel touch and pressure. They are thin and bendy, so they fit in small spaces. Many products use them for different jobs. Some examples are:
- Remote controls and smart appliances have pressure-sensing buttons.
- Handheld video games use force to make things happen.
- Electronic drum pads sense how hard you hit them.
- Phones and tablets have touch buttons for volume or power.
FSR sensors let devices know if you press soft or hard. One button can do more than one thing, depending on how hard you press. The sensors are very thin, less than 0.5 mm thick, so they fit in slim gadgets. They use little power, which helps batteries last longer. Because they are cheap and flexible, many new products use them.
FSR sensors help machines understand people better. They make devices smarter and easier to use.
Robotics
Robots use force sensing resistors to get better control and stay safe. Engineers put these sensors in robot fingers, feet, and bodies. This helps robots feel how much force they use right away. Robots can hold breakable things without breaking them. FSR sensors also help robots balance and walk by feeling pressure on their feet.
- Robots use force sensors to know when they touch things.
- The sensors are thin and light, so robots move fast.
- Using FSRs with other sensors helps robots feel more.
These things help robots work safely with people and do hard jobs. FSRs help robots grip better, balance, and work safely with humans. Robots become more careful and can do more things.
Medical Devices
Medical devices use force sensing resistors to help patients. Some sensors go inside the body to watch pressure and strain. These sensors send data to doctors right away, so they can check on patients. Special shoe insoles with FSRs measure foot pressure when walking. This helps doctors plan therapy for people with nerve problems.
Medical Device Type | Clinical Outcomes and Benefits |
---|---|
Cardiovascular screening tools | Helps doctors find and watch heart problems. |
Foot pressure measurement platforms | Helps treat foot problems and train walking. |
IVRA interface pressure sensors | Makes anesthesia safer by finding bad pressure. |
Implantable biosensors | Watches body pressure and strain to help patients. |
Wearable smart bandages | Finds pressure sores early and stops them from getting worse. |
Smart bandages with FSRs find pressure sores before they get bad. These sensors also help doctors spot problems during anesthesia by finding unsafe pressure. Using FSRs in healthcare makes treatments safer and helps patients get better.
Automotive
Cars use force sensing resistors to make driving safer and better. SOUSHINE FSRs are tiny and work well in cars today. Engineers put these sensors in seats, steering wheels, and control panels. The sensors help cars know what people are doing and what is happening.
- FSRs in seats check how weight is spread out. They can tell if a grown-up or a child is sitting there, with about 90% accuracy. This helps airbags open the right way for each person.
- Airbag systems use FSRs to see how hard a crash is. The sensors change how strong the airbag is, so people get hurt less.
- Driver help systems use FSRs in special controls. These controls help drivers steer, stop, or park with better feel.
- FSRs are small and cheap, so they fit in many car parts. They give quick data, so cars can react fast.
SOUSHINE has regular FSRs and resistive varistors for these jobs. The sensors help cars be safer and smarter. They also help car makers follow tough safety rules.
FSR technology helps cars become safer and smarter. The sensors work in both new cars and old ones.
Sensor Arrays
Sensor arrays use lots of FSRs together to get more pressure data. SOUSHINE sensor arrays help engineers and scientists see pressure on surfaces. These arrays are used in factories, labs, and smart products.
- FSR arrays make pressure maps for setting up machines and checking how they work. This helps factories run better and find problems early.
- The arrays help stop mistakes and keep things safe. They make sure machines do their job right every time.
- Using FSR arrays saves materials and money. Factories waste less and use less energy, which is good for the planet.
- In food packaging, FSR arrays check if seals are lined up right. This stops damage and keeps machines working.
- Car makers use FSR arrays to fit doors and hinges better. The sensors do the checking instead of people, so quality goes up and repairs go down.
- Robot hands with FSR arrays control how hard they grip. This lets robots hold things safely and work with people.
- FSR arrays give results that are right and can be repeated. They connect to software to help look at and study the data.
SOUSHINE sensor arrays come in many shapes and sizes. They help factories and labs do jobs better and make things higher quality. The arrays also help with research by giving clear and detailed data.
Sensor arrays with FSRs help factories and labs work better. They give the data needed for smart choices and safer products.
Connection and Usage
Circuit Setup
Engineers use a voltage divider circuit to connect a force sensing resistor. This setup uses the FSR and a fixed resistor together. It helps measure how much force is used. One end of the FSR goes to a voltage source, like 5 V or 3.3 V. The other end connects to an analog input pin. A fixed resistor, often 10 kΩ, goes from the analog pin to ground. When you press harder, the voltage at the analog pin goes up. The FSR does not care which way you connect it.
Application Type | Recommended Fixed Resistor Value |
---|---|
General use | 10 kΩ |
Light pressure detection | 47 kΩ |
Heavy pressure detection | 2 kΩ to 4.7 kΩ |
Picking the right resistor is important for good results. Choose a value close to the FSR’s middle resistance for best accuracy. Use a breadboard and jumper wires when testing your circuit. Do not solder straight to the FSR’s silver parts or you might break it. This simple setup is used in many FSR projects.
Tip: Try different resistor values to change how sensitive your sensor is.
Microcontroller Integration
Force sensing resistors work with microcontrollers like Arduino and Raspberry Pi. The voltage divider circuit links the FSR and a pull-down resistor in a line. The spot between them connects to an analog input pin. When you press harder, the FSR’s resistance drops and the voltage goes up. The microcontroller reads this voltage and turns it into a digital number.
With Arduino, connect the FSR and resistor as shown. Use analogRead() to get the voltage. You can use code to turn sensor values into force levels or control things like LEDs. For Raspberry Pi, you need an extra analog-to-digital converter because it does not have analog pins. This way, you can measure force in real time.
Note: Always check the FSR datasheet for the right resistor and wiring.
Demonstrations
Many projects show how flexible FSRs are. One project uses an FSR with an XBee radio to make a wireless force sensor. The setup has an XBee radio, FSR, 1 kΩ resistor, breadboard, jumper wires, and a DC power source. The FSR and resistor connect to the XBee board. The XBee radio reads the FSR and sends the data wirelessly. This shows how the FSR’s resistance changes with force and how you can send the data far away.
Other projects use Arduino to read force and control things like LEDs or motors. These examples help people see how FSRs work in real life. They also give ideas for using FSRs in new projects.
Measurement Tips
Getting good force readings means you need to be careful. Engineers and designers can use some simple steps to make force sensing resistor readings better:
- Install the Sensor Correctly
Put the force sensing resistor flat on the surface. Make sure it does not move around. If it is loose or on a bumpy spot, the results will not be steady. - Keep the Sensor Clean
Dust or dirt on the sensor can mess up the numbers. Wipe it with a soft, dry cloth to keep it working well. - Calibrate Frequently
Calibration helps the sensor give the right numbers. Press with known forces and change the system if needed. Do this often so the sensor stays correct as time goes by. - Test with Known Weights
Try using weights or special tools to check the sensor. This makes sure the sensor keeps working the same way every time. - Control Environmental Conditions
Heat and wet air can change how the sensor acts. Keep the sensor in a place where these things do not change much. If they do, fix the numbers to match. - Consider Mechanical Factors
The thickness of things on top of the sensor matters. The size of the spot you press also changes the reading. Use the same materials and press in the same way for best results.
Tip: Putting the sensor in the same way and checking it often helps it work well in any job.
Doing these things helps people get good results and makes the force sensing resistor last longer.
Testing and Troubleshooting
Common Issues
Force sensing resistors can sometimes give readings that jump around. This often happens if wires are loose or not connected well. Engineers should check every wire and connector to keep them tight. Changes in temperature can also make the sensor drift over time. Putting the sensor in a place where the temperature stays the same helps stop this drift. Using a temperature sensor nearby can help too. FSRs do not give a straight line response. Their readings curve, so it is hard to get exact force numbers, especially with strong pushes. Software tricks like special math or lookup tables can help fix this.
Other problems are noise and signals that change too much. Engineers can use moving average filters in the software to smooth out the numbers. Adding op-amp buffers and making the circuit better helps the sensor work well. Covers on top of the sensor stop damage from lots of pressing. Picking the right resistor for the voltage divider makes the sensor more steady and sensitive.
Tip: Check the sensor and wires often for loose parts or damage. Doing this simple check stops many problems before they start.
Calibration
Calibration makes sure the force readings from an FSR are correct. Engineers use known weights to make a calibration curve for each sensor. They check that all wires are tight and the voltage divider is set up right. The code must read the sensor and figure out resistance the right way.
To calibrate, follow these steps: 1. Put the FSR flat on a table. 2. Place known weights on it one by one. 3. Write down what the sensor shows for each weight. 4. Make a graph with these numbers to see the curve. 5. Change the software so it matches the curve.
Engineers should also fix for temperature changes by adding software tweaks. FSRs are best for seeing changes in force, not for measuring exact weights. Checking calibration often helps find drift and keeps readings true. Using good tools like multimeters and special resistors makes calibration better. Writing down calibration results helps with fixing problems later.
Maintenance
Regular care keeps FSRs working their best. Engineers should wipe the sensor with a soft, dry cloth to clean off dust. They should not use water or strong cleaners because these can hurt the sensor. Looking for cracks or worn spots helps find trouble early.
Covers or overlays help the sensor last longer, especially where it gets pressed a lot. Unused sensors should be kept in a dry, cool place to stop water damage. Testing the sensor with known weights often checks if it still works right. If the sensor drifts or acts strange, recalibration or getting a new one may be needed.
Note: Good care and checking calibration often help FSRs stay steady and work well in any job.
Force sensing resistors find force by changing resistance. They have a simple design that turns pressure into electric signals. Engineers use FSRs in robots, medical tools, cars, and gadgets. SOUSHINE has bendy choices for lots of projects.
See how SOUSHINE FSRs can help your next project. Reach out to the team for more info or check out all the products today.
FAQ
What is a force sensing resistor (FSR)?
A force sensing resistor finds force by changing resistance. When you press the sensor, resistance goes down. This helps show how much force is used.
How does an FSR connect to a circuit?
Engineers use a voltage divider to connect it. One side of the FSR goes to power. The other side connects to an analog pin and a resistor to ground. This setup lets devices see force changes.
Can FSRs measure exact weight?
FSRs show when force changes, not exact weight. They are best for finding touch or pressure. For exact weight, engineers use load cells or other sensors.
What is the typical response time for an FSR?
Most FSRs react in just a few milliseconds. This quick speed makes them good for things like touchpads or robots.
Where can engineers use SOUSHINE FSRs?
SOUSHINE FSRs work in electronics, robots, medical tools, cars, and sensor arrays. Their thin and bendy shape fits many projects.
How should users care for an FSR?
Keep the sensor clean and dry. Wipe it with a soft cloth. Do not use water or strong cleaners. Store unused sensors in a cool, dry place.
Do FSRs need calibration?
Yes. Calibration helps get correct readings. Users press known weights on the sensor and change the system to match.
Can FSRs bend or flex during use?
Yes. FSRs are flexible. They can bend to fit curved or small spaces and still work.