Call us: +86-137-2353-4866
Engineers pick force sensitive resistor fsr technologies by looking at how reliable they are, how much they cost, and if they fit the job. Resistive fsr types are most used for things people buy and for jobs that are not risky. Capacitive options work best for careful, factory jobs. The table below shows how much of the market each fsr product type has:
FSR Product Type | Market Share (%) |
---|---|
Round Force Sensing Resistors | 45 |
Square Force Sensing Resistors | 30 |
Strip Force Sensing Resistors | 15 |
Others | 10 |
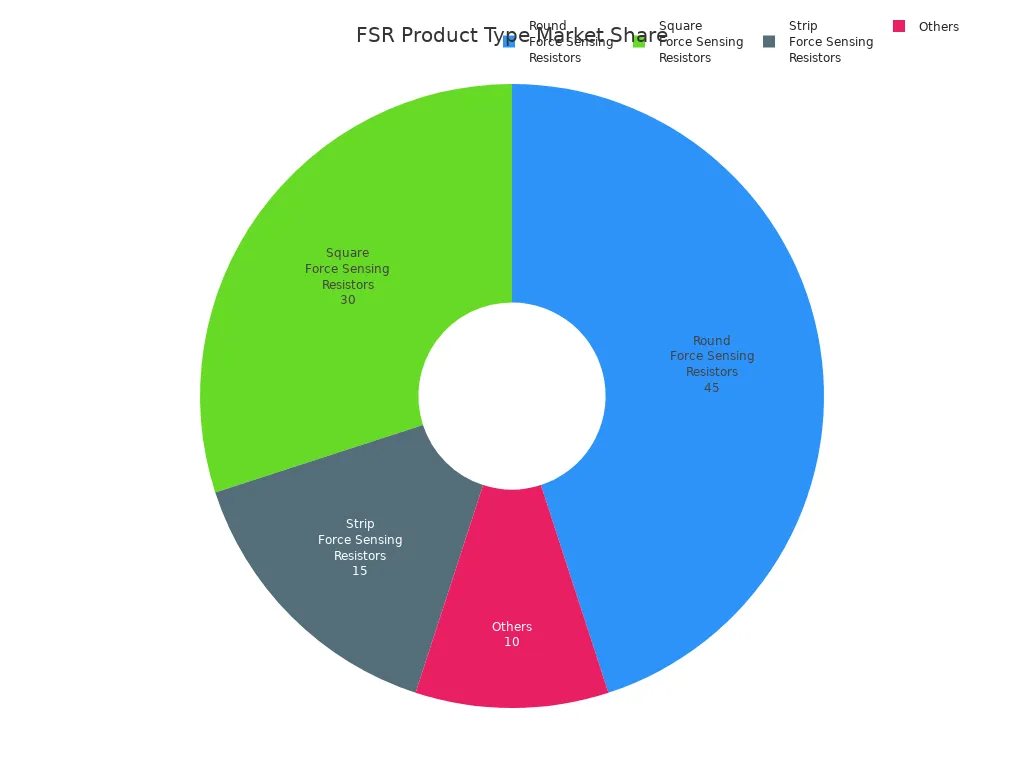
FSRs help make cars safer. They give live data in wearables. They also give touch feedback in robots. Engineers check fsr performance by looking at sensitivity, durability, response time, how easy it is to use, cost, and how many ways it can be used. New ideas in force sensing resistor and force sensor keep making force sensing technology and Force Sensing applications better.
Table of Contents
Key Takeaways
- FSRs change how much they resist electricity when pressed. They help measure force or touch in many devices. Engineers choose FSRs by looking at sensitivity, durability, response time, cost, and how easy they are to use. High sensitivity lets FSRs notice light touches. This makes measurements more accurate. Durability is important for using FSRs a long time. Some FSRs can handle millions of presses. Fast response time is needed for robots and interactive devices. These devices need quick readings. FSRs are thin and flexible. They are easy to connect to microcontrollers with a voltage divider. The price of FSRs is different. Cheaper FSRs save money but may not be as accurate or last as long. New FSR technologies use flexible materials and sensor arrays. These help FSRs work better in wearables and healthcare.
FSR Selection Criteria
Sensitivity
Sensitivity means how well an fsr can notice small force changes. Engineers want high sensitivity when they need to measure light touches. This is important for things like touch panels or medical devices. Sensitivity helps make fsr measurements more accurate. Thru Mode fsrs work better with light forces and give steady results. They do this no matter where you press on them. Shunt Mode fsrs can change more depending on where and how hard you press. Engineers must pick the right sensitivity for each project. High sensitivity gives better force measurement. Some fsrs, like Thru Mode types, have a more even response and less drift. This makes them good for jobs that need steady and repeatable results.
Note: Sensitivity is not only about finding force. It also helps the fsr tell apart different pressure levels in real life.
Durability
Durability tells engineers how long an fsr can last with lots of use. Most regular polymer thick film fsrs can take 100,000 to 1 million presses before wearing out. Some stronger types, like metalized or loaded PTF fsrs, last 10 million to 50 million cycles. How long an fsr lasts depends on its materials and how it is made. Pressing too hard or using it wrong can break the inside and make it wear out faster. The table below shows how long some fsrs last:
Product Model | Durability Rating (Actuations) |
---|---|
FSR406 | Over 10 million actuations |
Engineers should check durability ratings for projects that need lots of use. Picking a sensor with a high cycle rating helps fsrs work well for a long time.
Response Time
Response time is how fast an fsr reacts to force changes. Fast response times are needed for things like robots or interactive devices. Some fsrs, like Flexiforce A201, settle faster and have less drift. This makes them better for times when quick and steady readings are needed. The table below compares how fast different fsrs respond:
Aspect | Flexiforce A201 | Interlink 402 | Implications for Real-Time Applications |
---|---|---|---|
Static Compression Drift | 2–5x less drift | Higher drift | Flexiforce stabilizes faster, better for short-term |
Drift at 30s Loading | 1.8%–11.5% drift error | 8.2%–19.4% drift error | Interlink needs correction for dynamic scenarios |
Cyclic Loading Drift (1 Hz) | 6.00% drift | 10.26% drift | Flexiforce better for dynamic, real-time sensing |
A fast and steady response helps engineers get good fsr measurements when force changes quickly. Picking the right fsr for response time makes sure the device works well in tough situations.
Integration
Engineers like fsrs because they are easy to use. An fsr works with many microcontrollers, like Arduino. Most engineers use a voltage divider to connect an fsr. This circuit turns the fsr’s resistance into a voltage. The microcontroller can read this voltage. The voltage is usually between 1V and 5V. This matches what most microcontrollers need.
- An fsr is thin and can bend. It is only 0.2mm to 1mm thick.
- The resistance of an fsr is high with no force. It drops to a few hundred ohms with lots of force.
- Engineers must pick the right resistor for the voltage divider. This helps get the best sensitivity.
- Calibration or software can fix the fsr’s non-linear response.
- An fsr reacts fast, so it works well in real-time.
- You can put an fsr on hard or soft surfaces.
Tip: Always calibrate the fsr in the final device. This helps you get correct readings.
Cost
An fsr does not cost much compared to other force sensors. Many fsrs use cheap materials like Velostat. This makes fsrs good for products and research. But cheaper fsrs may not be as accurate or repeatable. Some fsrs can have errors up to 15%. Engineers must think about cost and performance for their project. For big orders, fsrs save money. But engineers should test if the fsr stays stable in their device.
FSR Type | Typical Unit Cost | Performance Notes |
---|---|---|
Standard FSR | Low | Lower repeatability |
Custom FSR | Low to Moderate | Varies by material quality |
Versatility
An fsr can be used in many areas. Its thin and bendy shape is good for robots, medical tools, and electronics. In robots, an fsr helps with grip and safety. Medical tools use fsrs to check pressure in beds or prosthetics. Electronics use fsrs for touch buttons and smart clothes.
- An fsr works on hard and soft surfaces.
- Engineers can use fsrs with other sensors, like biometric sensors or heaters.
- An fsr uses little power and senses small force changes.
- Its simple shape makes it easy to add to new products.
An fsr can do many jobs. This makes it a good pick for engineers who want a flexible and reliable force sensor.
Force Sensitive Resistor FSR Technologies
Interlink FSR 400
The Interlink FSR 400 is a popular force sensitive resistor fsr. Engineers like it because it is easy to use and strong. This fsr has one sensing area and is very thin. It can sense forces as small as 0.1 N and up to 10 N. It works the same way every time and lasts a long time. This makes it good for tough places.
Feature / Specification | Details |
---|---|
Sensor Type | Single zone Force Sensing Resistor (FSR) |
Sensor Size | Standard: 7.62 mm diameter; Customizable: 5 mm to over 600 mm |
Thickness | Ultra-thin profile, approximately 0.35 mm |
Actuation Force | As low as 0.1 N |
Sensitivity Range | Up to 10 N |
Repeatability | Variation as low as 2% |
Durability | Up to 10 million actuations |
Variants | Female connector and short tail versions available |
Construction | Robust polymer thick film (PTF) device |
Common Applications | Automotive electronics, medical systems, industrial and robotics, game controllers, musical instruments, remote controls, navigation electronics, industrial HMI, automotive panels, consumer electronics |
Integration | Simple and easy to integrate |
Many engineers pick the Interlink FSR 400 because its fsr resistance changes are easy to predict. It can handle shocks well. The sensor does not get messed up by electromagnetic interference or static electricity. It does not cost much and is easy to find. People use it in things like car panels, remote controls, and other electronics.
Advantages of Interlink FSR 400:
- Easy to add to many devices
- Lasts a long time and is strong
- Very thin shape
- Can sense a wide range of forces
- Not bothered by EMI or ESD
- FSR resistance changes are steady
- Low price and easy to buy
- Handles shocks well
Ohmite FSR
Ohmite FSR products change resistance when you press on them. This helps measure force and gives touch feedback. The sensor gives an analog signal, so engineers can see force changes right away. Ohmite fsr sensors work in cold and hot places, from -20°C to 85°C. They do not get damaged by water. These sensors follow RoHS3 rules and are still being made.
Characteristic / Metric | Description / Value |
---|---|
Sensor Type | Resistive Force-Sensing Resistor (FSR) with dynamic resistance varying by applied force |
Output Type | Analog output for precise measurement and control |
Operating Temperature Range | -20°C to 85°C |
Moisture Sensitivity Level (MSL) | 1 (Unlimited) – high resistance to moisture |
RoHS Compliance | ROHS3 Compliant |
Part Status | Active production |
Termination Style | Connector |
Applications | Industrial automation, medical devices, consumer electronics, robotics, home automation |
Embedded Modules | Microcontroller boards, industrial control systems, gaming consoles |
Alternative Models | FSR02CE, FSR03CE with different sensitivity levels |
Ohmite fsr sensors are best when you need to know if force is there and how strong it is, not the exact weight. Engineers use them in small electronics, games, and phones. In medicine, the FSR03CE model helps check heart and breathing rates. The sensor’s force and conductance change together in a straight line. A special circuit keeps the readings steady. This makes Ohmite fsr sensors great for careful force sensing in medical and home devices.
Tekscan FlexiForce
Tekscan FlexiForce sensors are used a lot in medical tools. They are thin, bendy, and light, so they fit in many devices. Engineers put them in surgery robots to give touch feedback. This helps doctors do careful and gentle surgeries. Rehab tools use FlexiForce sensors to help people get stronger hands.
FlexiForce sensors give numbers that help doctors treat patients better. They are also used in new products that need good force sensing. These sensors work in many different projects that need to measure force well.
Key applications for Tekscan FlexiForce:
- Medical tools and surgery devices
- Rehab tools for hand exercises
- OEM and built-in force sensor uses
- Robotics and new product designs
Tekscan FlexiForce sensors give steady fsr resistance changes and work for many force sensing technology needs. Their good performance and flexibility make them a top pick for engineers in health care and new product design.
SOUSHINE FSR
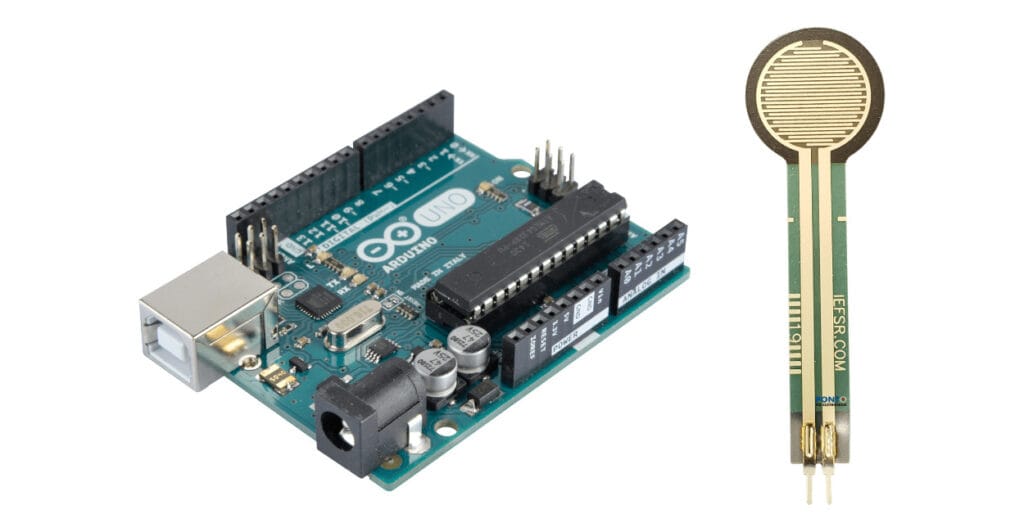
SOUSHINE FSRs are changing force sensing technology. The company uses a special polymer film with tiny conductive particles. These particles are smaller than a micrometer. They help the sensor notice small force changes. When you press on the sensor, a conductive ink spreads out. This makes more contact and lowers resistance. It also helps the sensor last longer.
The SOUSHINE fsr has two membrane layers and a circuit. This makes it stronger and better with heat. Engineers can use these sensors for over 10 million presses. The piezoresistive design lets the fsr measure small force changes well. This is good for careful jobs in healthcare and robotics.
SOUSHINE fsr products are not just single-point sensors. The company also makes sensor arrays. These arrays help engineers measure many forces at once. The sensors stay flexible and strong. This makes them great for wearables and bendable electronics.
Note: SOUSHINE fsr sensors use new materials and ways to make them. These changes lower signal drift and make them more reliable. Engineers can use these sensors in smart devices and AI systems without worry.
Key advantages of SOUSHINE FSR:
- High sensitivity from advanced polymer and conductive ink design
- Long lifespan with over 10 million actuations
- Flexible and durable for wearable and bendable electronics
- Accurate detection of small force changes
- Reliable performance in healthcare, robotics, and smart devices
Engineers pick SOUSHINE fsr sensors for projects that need accuracy, flexibility, and long life.
Emerging FSR Solutions
The fsr market is growing with new materials and designs. Thin film, flexible, and textile-based fsr types are leading new ideas. These use special composites and nanofibers to get better sensitivity and strength.
Trend / Aspect | Description / Findings |
---|---|
Thin Film FSR Calibration | High linearity and repeatability; calibration equations improve precision and reliability. |
Conducting Polymer Composites | Composites like PVA/CNT/PANI increase flexibility and mechanical strength. |
Sensitivity and Durability | Nanofibers and polymers boost sensitivity and reduce hysteresis. |
Creep and Sensitivity Degradation | Proper voltage selection reduces sensitivity loss over time. |
AC Electrical Field Application | Sensors respond faster and with higher sensitivity under AC fields. |
Nanofiber and Textile-based Sensors | Flexible, wearable electronics use nanofiber and textile-based fsr devices. |
Application Areas | Healthcare, robotics, and human-machine interfaces benefit most from these advances. |
Flexible and wearable fsr sensors are now important in healthcare and robotics. Engineers use stretchable filament sensors that act like muscles and tendons. These sensors turn force into hydraulic pressure inside a fiber channel. The design lets you change sensitivity and is easy to make.
Aspect | Description |
---|---|
Sensor Type | Stretchable filament sensor (SFS) |
Working Principle | Converts force into hydraulic pressure in a fiber channel |
Key Features | Tunable sensitivity, scalable, soft, stretchable, low cost |
Healthcare Applications | Motion tracking gloves, smart garments, surgical tools |
Robotics Applications | Teleoperated surgical systems, wearable robotics |
Advantages | Maintains flexibility, does not add rigidity |
Limitations | Hysteresis increases with pressure, strain limits exist |
Significance | Enables closed-loop control in prostheses and rehabilitation aids |
Flexible wearable fsr sensors help with real-time checks in medical and robotic systems. Engineers use materials like polydimethylsiloxane, hydrogels, and conductive polymers. These sensors block electromagnetic interference and work with machine learning and IoT. They are used for breathing checks, muscle tracking, and smart clothes.
Tip: Engineers should think about how to connect, keep stable, and save energy when picking new fsr technologies for wearables or robots.
The fsr world now has thin film, flexible, and textile-based sensors. These new types help engineers make devices that are more flexible, reliable, and ready for modern healthcare and robotics.
FSR Comparison
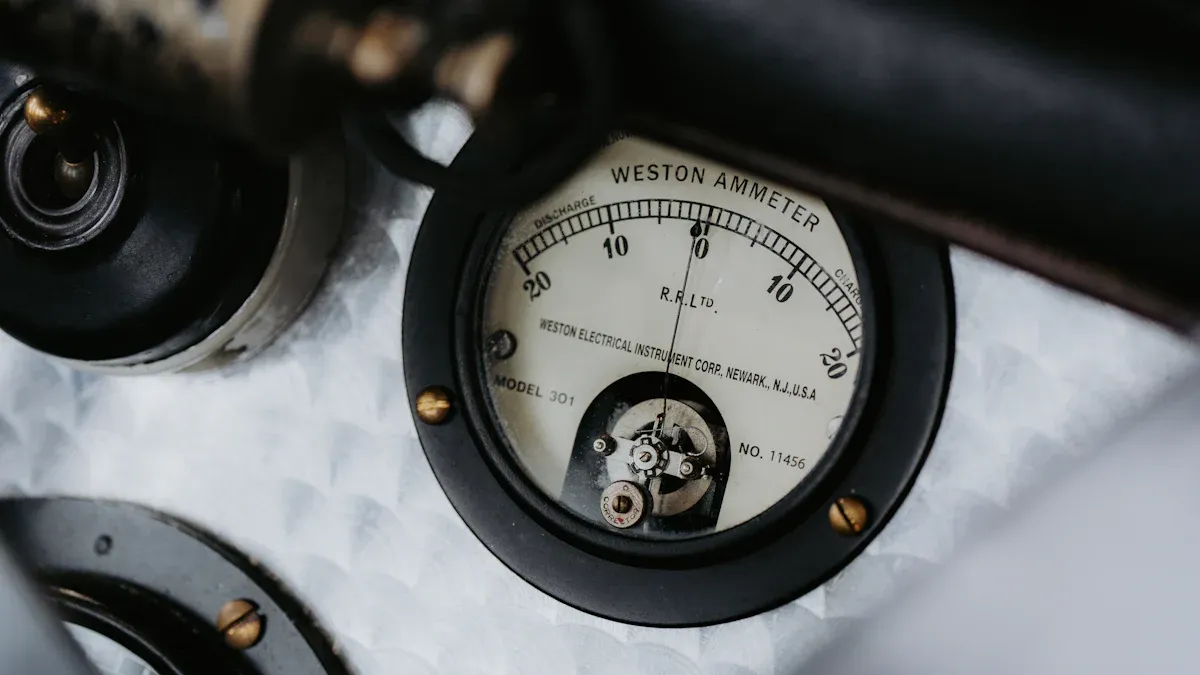
Comparison Table
Engineers look at sensitivity, cost, and how easy fsrs are to use. They also check if the fsr fits the job. The table below shows how top fsr products compare. This helps engineers pick the best force sensor for their work.
Product | Sensitivity | Cost | Integration | Application Fit |
---|---|---|---|---|
Interlink FSR 400 | Moderate, stable | Low | Simple, thin, flexible | Automotive, consumer electronics |
Ohmite FSR | Moderate, analog | Low | Easy, robust | Medical, industrial, robotics |
Tekscan FlexiForce | High, customizable | Moderate | Flexible, matrix possible | Medical, rehab, robotics |
SOUSHINE FSR | High, precise | Low/Moderate | Flexible, sensor arrays | Wearables, healthcare, AI |
Hobbyist FSRs | Tunable, limited | Very Low | Simple, breadboard | Prototyping, education |
Hobbyist fsr sensors cost about $10 each. They use a simple voltage divider to connect. You can change the resistor to adjust sensitivity. But these fsrs are not as accurate as industrial ones. Industrial fsrs like SOUSHINE and Tekscan are more accurate and last longer.
Strengths and Weaknesses
Every fsr type has good points and bad points. Engineers should think about these before picking a force sensor.
FSR Type | Strengths | Weaknesses |
---|---|---|
Off-the-shelf FSRs | Easy to find, simple to use | Can break over time, not washable, may give false positives |
Textile-based FSRs | Good for wearables, flexible | Lower conductivity, less robust than embroidered types |
Embroidered Textile FSRs | High conductivity, strong, washable, works in tough conditions | Needs special equipment, more complex to make |
General FSR Technology | Flexible formats, fits many designs | Limited force range, accuracy issues, can be hard to integrate |
Thru mode fsrs like Tekscan FlexiForce are flexible and easy to change. Shunt mode sensors act differently with drift and linearity. This changes fsr resistance and measurements. Off-the-shelf fsrs are good for simple jobs but may not last in hard places.
Best Use Cases
Engineers pick fsr models for different jobs. Some fsrs work better in certain places.
- For very accurate jobs, engineers use strain gauges or load cells instead of fsrs.
- For cheap projects, fsrs are a good choice. They are thin, bendy, and fit in small spaces.
- In tough places, Interlink FSR 400 and similar types handle dust and heat well.
- SOUSHINE fsrs are best for wearables, healthcare, and AI. Their sensor arrays help map force in detail.
- Tekscan FlexiForce sensors are great for medical and rehab tools. Their flexible shape fits in tight spots.
- Hobbyist fsrs are best for learning and testing ideas. Students use them to learn about force sensors.
Tip: Engineers should use the right fsr testing for each job. This helps get good fsr resistance readings and correct measurements.
Force Sensitive Resistor Selection Guide
Application Needs
Engineers first decide what the project needs. Every project is different. Some devices must sense light touches. Others need to feel strong pressure. Engineers check the force range and the size of the sensing area. They also look at what kind of output signal is needed. For example, a medical device may need high sensitivity for gentle touches. An industrial machine may need a sensor for heavy, repeated use. The shape and size of the fsr are important too. Round, square, and strip fsrs fit different spaces. Engineers think about how the fsr will work with other parts. Wearable devices need fsrs that are flexible and comfortable. In robots, the sensor must react fast and fit in small spaces. Engineers also ask how often the sensor will be used. Sensors for lots of use must last a long time. Picking the right fsr for the job helps the project work well.
Environment Factors
The place where the fsr is used matters a lot. Temperature, humidity, and stress can change how the sensor works. When you press on the fsr, stress changes the contact resistance inside. This affects the sensor’s output. If the stress bends the sensor too much, the contact area gets bigger. This can help conduction, but resistance may not change evenly. Engineers must think about these things when testing fsrs. High heat can make the sensor less able to sense force. Studies show that higher temperatures lower the sensor’s ability to sense stress. Humidity can also change how the sensor works, but it is harder to predict. Sometimes, humidity changes the electrical resistance and the readings. Engineers should protect the fsr from harsh conditions. Good covers and seals help keep the sensor working right. By knowing these things, engineers can pick the best fsr for tough places.
Budget Considerations
Money is important when picking sensors. FSRs are a cheap way to measure force. Engineers compare prices and think about what they need. Standard fsrs cost less and are good for simple jobs. Custom or special fsrs cost more but work better and last longer. Engineers also look at the total cost, like putting in and fixing the sensors. Some projects need many sensors, so price per sensor matters. When making a budget, engineers think about how long the fsr will last. A sensor that lasts longer can save money later. By thinking about cost and how well the fsr works, engineers pick the best one for their project.
Selection Steps
Engineers use simple steps to pick the right fsr. Each step helps make sure the sensor works well for the job.
- Define the Force Range
Engineers write down the smallest and biggest forces the fsr must sense. This helps them choose the best sensor. - Choose the Sensing Area
The fsr’s size and shape are important. Round, square, or strip sensors fit different spots. Engineers pick what fits the device. - Check Sensitivity and Response Time
Some jobs need the fsr to feel soft touches. Others need it to react fast. Engineers look at datasheets to find the right one. - Evaluate Durability
Projects used a lot need a strong fsr. Engineers check how many times the sensor can be pressed. - Assess Integration Needs
Engineers see how easy it is to connect the fsr. They check if it works with the microcontroller or circuit. - Consider Environmental Factors
Heat and wetness can change how the fsr works. Engineers pick sensors made for those places. - Review Cost and Availability
Engineers look at prices and see if the fsr is easy to buy. They also think about future costs. - Test and Calibrate
Before using it, engineers test the fsr in the real device. Calibration helps get correct numbers.
Tip: Trying an fsr in a test device helps engineers find problems early.
Common Mistakes
Engineers sometimes make mistakes when picking or using an fsr. Avoiding these mistakes helps projects work better.
- Ignoring Force Range
Some engineers pick an fsr without checking if it senses the right force. This can give bad results. - Skipping Calibration
Not calibrating the fsr makes the data wrong. Each sensor can act a little different. - Overlooking Environmental Effects
Not thinking about heat or wetness can make the fsr drift or stop working. - Improper Mounting
Putting the fsr on bumpy or soft places changes how it works. Engineers should follow mounting rules. - Neglecting Integration Details
Not planning how to connect the fsr can slow down projects. Engineers should check if it fits the circuit early.
Mistake | Impact | Solution |
---|---|---|
Wrong force range | Bad readings | Pick fsr for the job |
No calibration | Unsteady output | Always calibrate |
Bad mounting | Sensor breaks or drifts | Use flat, hard surfaces |
Ignoring environment | Sensor stops working | Pick the right fsr |
Poor integration plan | Delays and more costs | Plan for circuit fit |
Note: Good planning and testing stop most fsr problems.
Engineers need to pick a force sensitive resistor fsr that fits what their project needs. They should think about how much the sensor can change and if it works for the job. To make sure the force sensitive resistor works well, engineers must calibrate it carefully. They also need to pick the right resistor to use with it and watch for differences between each sensor.
- FSRs are good for measuring if force is there or not and for designs that need to bend or change shape.
- Learning about new sensor technology helps engineers do better work.
- Talking to suppliers helps engineers find the best sensor for what they need.
FAQ
What is a force sensitive resistor (FSR)?
A force sensitive resistor can sense force or pressure. Its resistance changes when you press on it. Engineers use FSRs in many devices to measure touch.
How do engineers connect FSRs to microcontrollers?
Engineers use a voltage divider circuit to connect FSRs. They put the FSR and a resistor in a line. The microcontroller checks the voltage between them to measure force.
Can FSRs measure exact weight?
FSRs cannot measure exact weight. They only show changes in force or pressure. For exact weight, engineers use load cells or strain gauges.
Where do engineers use FSRs most often?
Engineers use FSRs in robots, medical tools, cars, and electronics. FSRs help find touch, grip, or seat pressure.
How long do FSRs last?
Most FSRs last through millions of presses. How long they last depends on the material and how much force is used.
Do FSRs work in wet or hot environments?
Some FSRs can work in wet or hot places. Engineers should check the product’s specs for temperature and moisture limits.
What is the difference between shunt mode and thru mode FSRs?
Shunt mode FSRs change resistance based on where and how hard you press. Thru mode FSRs give more even results across the whole sensor.
How do engineers calibrate an FSR?
Engineers press known weights on the FSR and write down the output. They use this data to make a calibration curve for better readings.